Bearings are an indispensable part of almost all industrial machinery, household appliances, automobiles, construction equipment, and nearly everything – that has a moving part. From the smallest applications in fidget spinners to utilisation in wind turbines, bearings are everywhere.
Wind power is expanding globally due to increasing environmental concerns, technological advancements, government policies, cost-effectiveness, and more. Wind power is generated by wind turbines, which are gigantic machines equipped with a rotor hub. These turbines can weigh over 200 tons and are fitted with bearings to support the rotating shaft and allow the turbine to operate smoothly. Several types of bearings are used in wind turbines including, spherical roller bearings, tapered roller bearings, cylindrical roller bearings, deep groove ball bearings, and more.
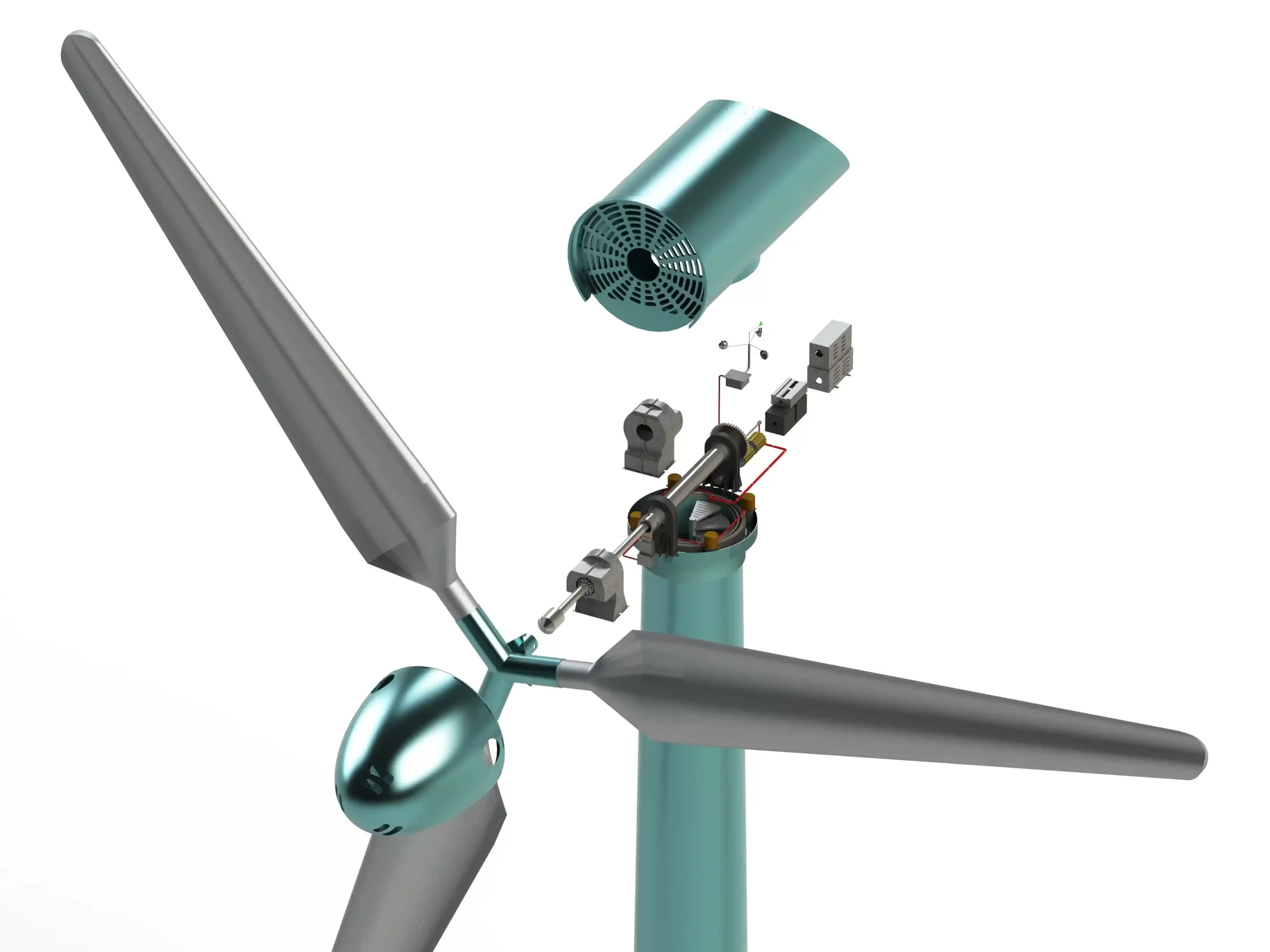
India’s wind energy sector accounts for 10.5% of total power generation, additionally, India aims to generate 50% of the electricity from green sources by 2030. The growth and expansion are highly dependent on the wind energy sector and necessitate the need for high-quality bearings that can sustain high loads, dynamic loads, and more.
Role of Bearings in Wind Turbine Efficiency
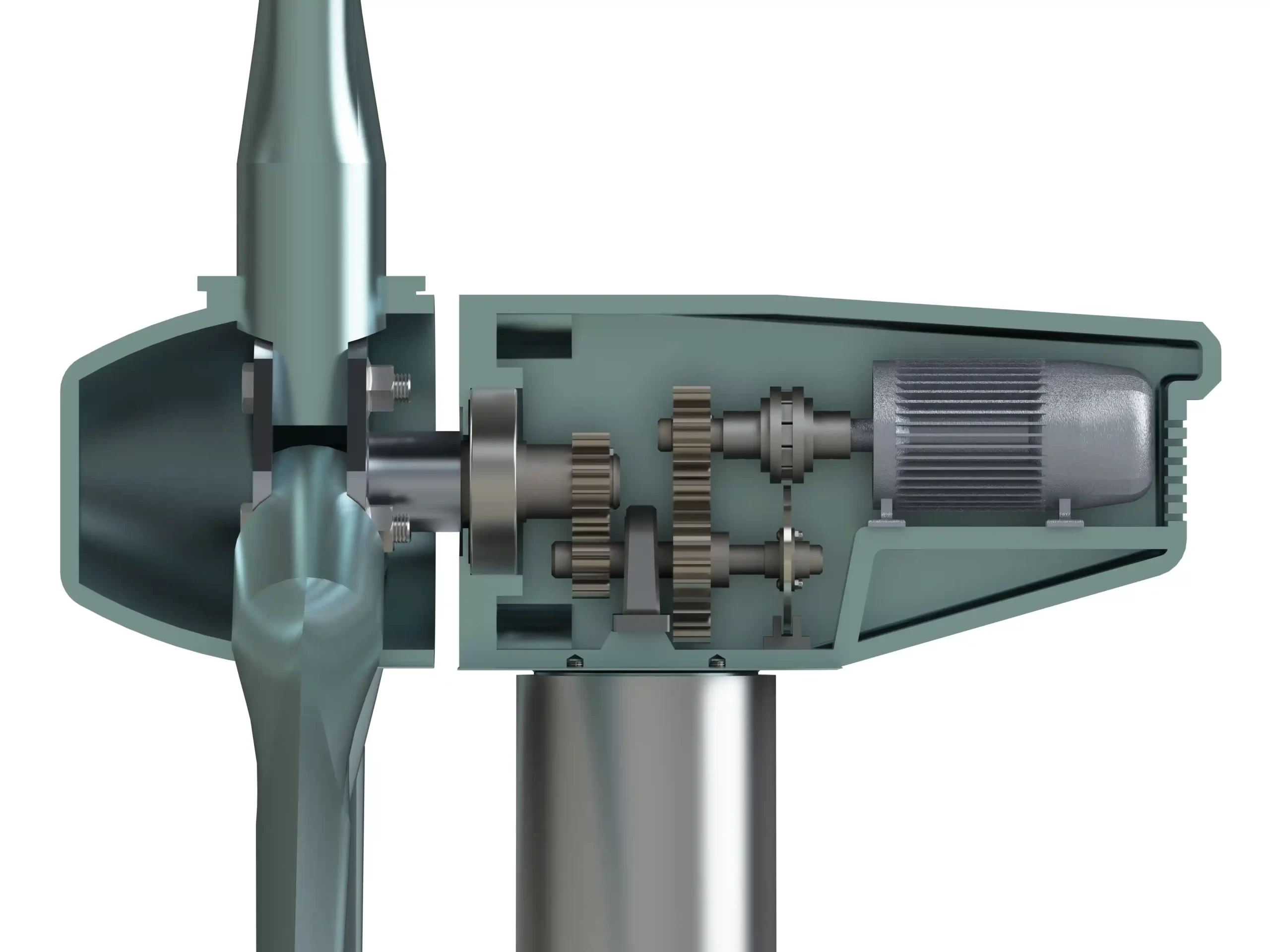
Wind turbines are equipped with various bearings used in each section including the pitch and yaw location, main shaft location, and gearbox. These bearings are responsible for the efficiency, reliability, and lifespan of wind turbines. Bearings play a crucial role in ensuring smooth power transmission and supporting the rotating components. The impact of bearings on wind turbine efficiency includes:
- Reduce Friction: The primary role of bearing in wind turbines is to reduce friction between the moving parts, leading to reduced energy loss and improved overall efficiency.
- Load Support: Bearings in wind turbines play a crucial role in supporting wind turbines as they operate under fluctuating loads due to speed variations. Bearings play an essential role in distributing the load evenly resulting in stable operation.
- Support Rotation: Bearings are fitted in the rotor and gearbox and ensure smooth rotation and efficient power transmission. High-quality bearings are critical for optimum turbine efficiency and lifespan.
Types of Bearings Used In Wind Turbines
Several types of bearings are fitted into wind turbines to perform different functions. Here is a rundown of some of the most common bearings within wind turbines:
Such bearings are widely preferred for gearboxes and generators. Cylindrical roller bearings are designed to handle high-radial loads generated by the turbine’s gearbox and generator making it ideal for demanding conditions.
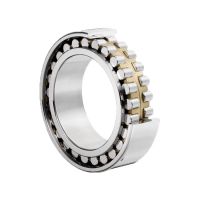
Spherical roller bearings are usually found in the main shaft of the turbine. These bearings are designed to handle high-radial and axial loads at low to medium speeds.
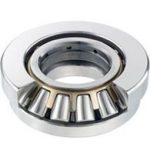
Tapered roller bearings are fitted in wind turbines to handle tilting movements. These bearings are usually custom-designed and are commonly used in gearboxes to handle high vibration levels.
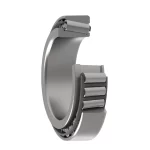
Deep Groove Ball Bearings
Commonly used in generators and electric motors to handle medium to high radial and axial load, deep groove ball bearings hold weight in loads in both directions.
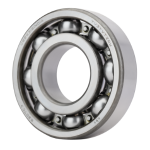
Bearing Technologies for Wind Turbines
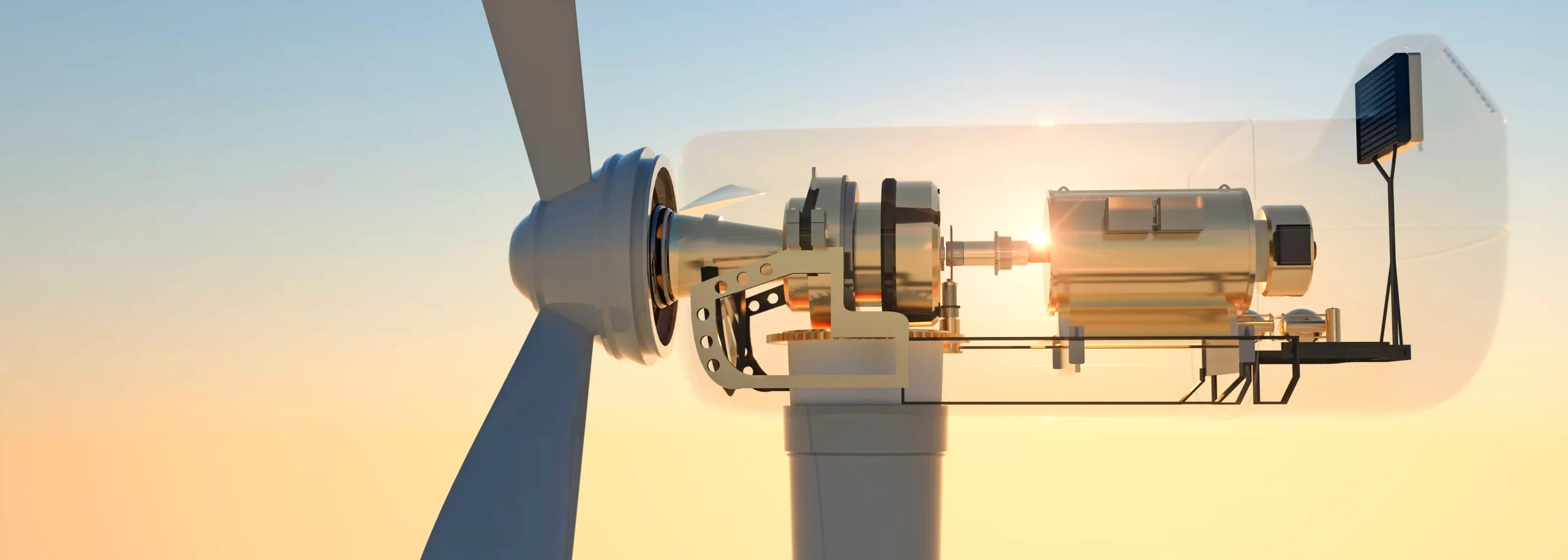
Wind energy is emerging as a significant source of clean electricity. Wind turbines are fitted with various components that allow for effective energy generation, one such crucial component is the bearing system. The bearings fitted in wind turbines operate under extreme conditions including:
- High Loads (rotor weight, dynamic load due to wind speed variations)
- Harsh Environmental Conditions (temperature variations – deserts, arctic regions)
- Maintenance Challenges (remote locations and size of wind turbines)
However, the wind turbine sector continues to expand necessitating the need for further improvements in the bearing technology.
Technologies Used in Wind Turbines
- Coating: Bearing technologies like black oxide coating help prevent components from corrosion and other environmental damages, thus enhancing lifespan.
- Monitoring Tool: Allows for monitoring and predicting issues before complete failure impacting operation. Monitoring technology reduces the risk of damages, increases turbine uptime, and allows for planned maintenance.
- Lubrication: Bearing technologies like self-lubricating bearings and lubricants resistant to corrosion and wear limit friction and increase the overall life of bearings.
Maintenance of Wind Turbine Bearings
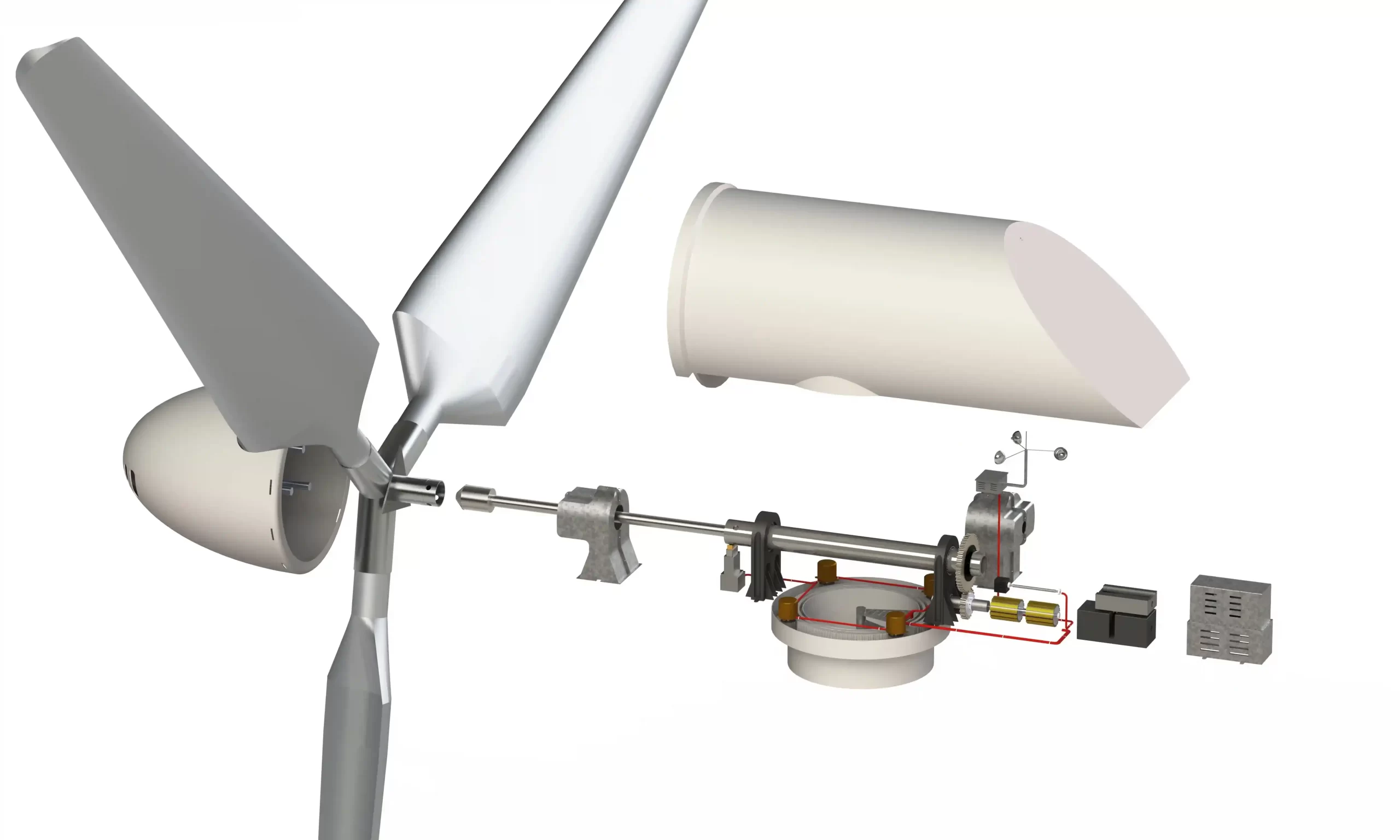
- Lubrication Management: Lubrication plays a key role in the maintenance of wind turbine bearings. Greasing at periodic intervals and using high-quality lubricants formulated for extreme temperatures minimises friction and wear.
- Inspection: Bearings must be checked for damages, cracks, and scoring during routine maintenance. Additionally, temperature and vibration monitoring may be performed to check for misalignment, overheating issues, etc.
- Predictive Maintenance: Tools like advanced monitoring systems help predict bearing damage or failure based on vibration patterns, wind speed, and temperature trends. Predictive maintenance techniques eliminate unexpected breakdowns of wind turbines.
- Replacement: The bearings in wind turbines must be replaced on their expected lifespan or when there’s a sign of wear or damage. Additionally, proper installation with specialised tools must be done to avoid misalignment and premature failure.
FAQ's
What are the bearings used in wind turbines?
Several types of bearings are used in wind turbines including cylindrical roller bearings, tapered roller bearings, deep groove ball bearings, etc.
What 2 types of bearings are in a turbine engine?
Spherical roller bearings and cylindrical roller bearings are most commonly used in turbine engines.
How long do wind turbine bearings last?
The lifespan of turbine bearings depends on various factors including operational environment and maintenance. Usually wind turbine bearings last 20 years.