In the labyrinth of the machinery ecosystem, bearings emerge as silent architects, orchestrating the efficiency and functionality of diverse equipment across industries. Let’s delve into the nuanced world of bearings and their profound impact on machine efficiency, exploring the intricacies of bearing friction, the battle against contamination, and the role of precision design in achieving optimal efficiency.
Overview: Role of Bearings in Equipment Efficiency
Bearings, often inconspicuous in their presence, play a pivotal role in
- Determining the efficiency of machinery
- Serving as the interface between moving parts
- Ensuring smooth operation and
- Minimizing energy losses.
Therefore understanding their role is fundamental to appreciating their impact on overall equipment efficiency. Picture a conveyor system in a manufacturing plant. The efficiency of this system relies on the seamless rotation of its components, facilitated by bearings. Efficient bearings translate into a conveyor system that operates smoothly, minimising energy consumption and maximising productivity.
Does Bearing Friction Directly Impact Energy Usage?
Friction, the inherent nemesis of machinery, can impede efficiency and escalate energy consumption. Bearings act as protective guardians against such excessive friction, ensuring that moving parts glide with minimal resistance.
Visualise a wheel on a moving vehicle. Without bearings, the friction between the axle and wheel would be substantial, demanding more energy to overcome this resistance. Bearings reduce this friction, allowing the wheel to rotate with ease and minimising the energy required for movement. This is further dependent upon the type of friction, i.e., whether this is rolling friction or sliding friction.
The choice between rolling and sliding friction is a critical design consideration in bearing efficiency. Rolling friction, prevalent in ball and roller bearings, is inherently lower than sliding friction, reducing energy losses and enhancing overall efficiency.
For example: A door hinge – an example of sliding friction. Skateboard’s wheels – an example of rolling friction. Bearings in the skateboard wheels facilitate smooth rotation with minimal friction, contributing to energy-efficient movement.
How Does Bearing Friction Impact Each Component?
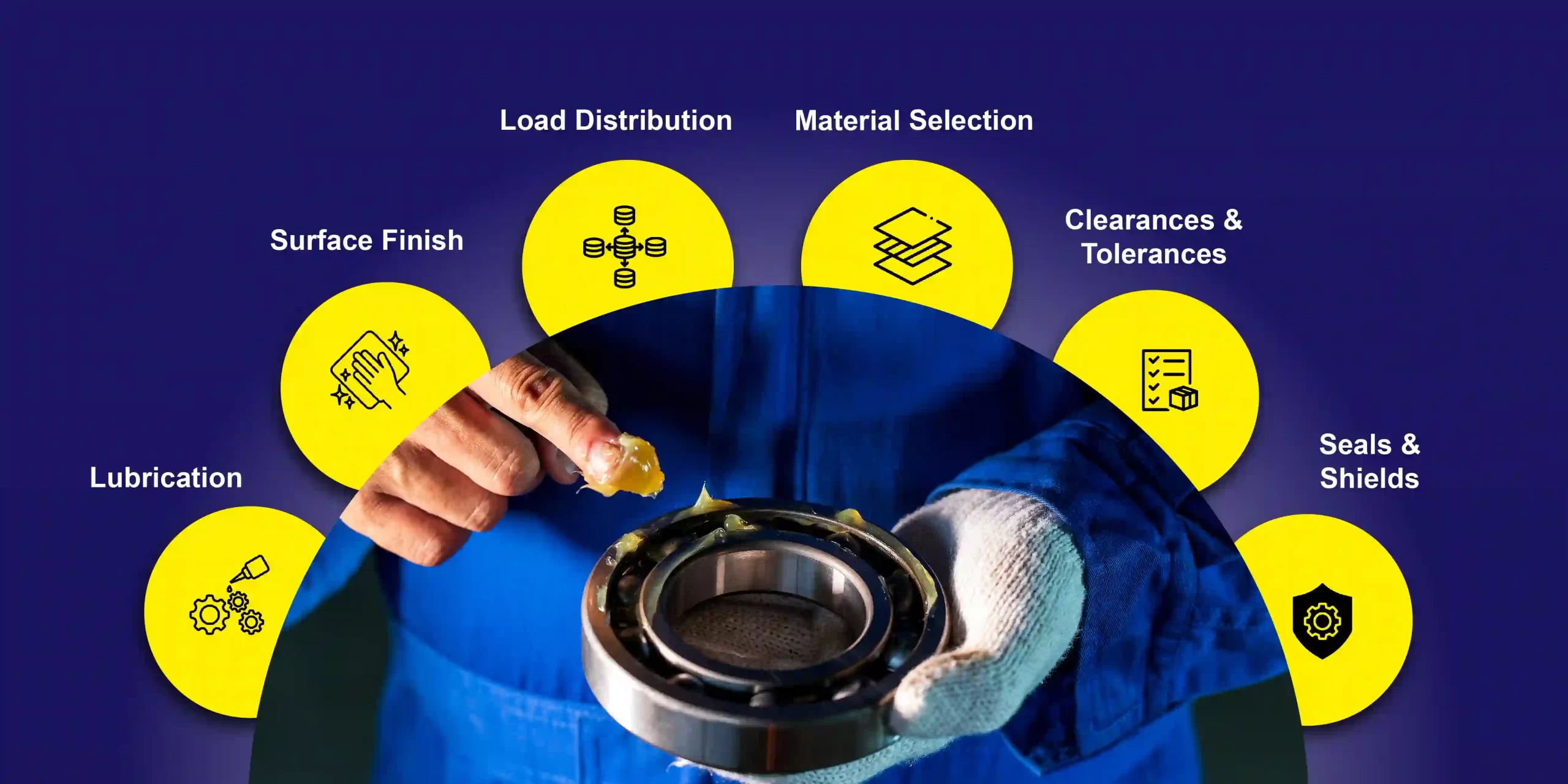
Understanding the intricate dynamics of bearing friction involves delving into the various components that contribute to this critical aspect of mechanical performance. Bearing friction is a complex interplay of factors, each influencing the overall efficiency and functionality of the bearings. Let’s break down the key components:
- Lubrication: It involves the application of a lubricant, typically oil or grease, to reduce friction and wear between bearing components. For example: ball bearings in a car wheel, when receiving adequate lubrication, ensure that the rolling elements (balls) move smoothly within the raceways, minimising friction and extending the life of the bearing.
- Surface Finish: The surface finish of bearing components such as raceways and rolling elements, significantly impact friction. A smoother surface finish reduces contact resistance and contributes to lower friction levels. Example: a needle roller bearing in a precision instrument performs smooth and precise rotational action with minimal friction in a highly smooth surface finish.
- Load Distribution: Proper load distribution across bearing elements is crucial for managing friction. Uneven loading emphasises localised stress and increased friction, pulling down overall efficiency of the bearing. Example: In a tapered roller bearing used for a vehicle’s wheel hub, the design ensures that the load from the vehicle’s weight is distributed evenly across the rollers, preventing excessive friction and promoting efficient rotation.
- Material Selection: The choice of materials for bearing components, such as steel alloys or ceramics, influences friction. Each material has unique properties that impact factors like heat generation and wear resistance. Example: thrust ball bearings in an industrial gearbox are made of material composition tailored to withstand high axial loads while maintaining minimal friction.
- Clearances and Tolerances: The clearances and tolerances between bearing components play a critical role in managing friction. Precision in manufacturing ensures proper fitment, minimising unnecessary friction. Example: A cylindrical roller bearing in a conveyor system. The meticulous control of clearances and tolerances ensure smoothness within the bearing, reducing friction and enhancing efficiency.
- Seals and Shields: Bearing seals and shields protect against external contaminants, preserving the integrity of the lubricant and preventing friction-inducing particles from entering the bearing. Example: A deep groove ball bearing in an electric motor needs protection from dust or moisture to prevent compromising lubrication necessary for a friction-free environment.
Visualise a high-speed spindle in a machining centre. The bearings supporting this spindle operate under immense loads and speeds. Proper lubrication, precise surface finishes, and optimal load distribution are critical factors ensuring minimal friction and, consequently, high efficiency.
How Does Contamination Accumulation Accelerate Wear?
Contamination, a perpetual adversary in machinery, poses a threat to bearing efficiency. Particles like dust and debris compromise the smooth operation of bearings, leading to increased friction, wear, and a subsequent drop in efficiency.
For example: Consider a wind turbine in a dusty environment. Without effective seals and maintenance, bearings in the turbine would accumulate contaminants, compromising their efficiency over time. Proper preventive measures are essential to maintain optimal efficiency.
This is where bearing design plays a pivotal role. Factors such as material selection, geometry, and load-bearing capacity influence the overall performance of bearings, directly impacting the efficiency of the machinery they support.
For example: In the case of a robotic arm in an automotive assembly line, the precision required in the arm’s movements demands bearings with optimised designs crafted to ensure high efficiency, and seamless operation.
Quantify Efficiency Losses & Adopting Precision Based Manufacturing Methods
Engineers employ various methods to quantify efficiency losses attributed to bearing friction. Calculations consider factors such as load, speed, and lubrication to determine the overall impact on energy consumption.
Imagine an electric motor powering an industrial fan. Bearings in the motor influence its efficiency. Through calculations, engineers assess the impact of bearing friction on the motor’s overall efficiency, allowing for informed decisions on design and lubrication.
With the help of careful assessment, these parts evolve towards the formation of precision based manufacturing methods. These methods employed in bearing production significantly impact their efficiency. Precision machining and advanced manufacturing techniques ensure that bearings meet stringent tolerances, reducing variability and enhancing their overall efficiency.
Imagine a high-speed spindle in a CNC machine. The bearings supporting this spindle undergo precision manufacturing processes to achieve exacting tolerances. This precision ensures minimal variability, contributing to the efficiency of the entire machining process.
FAQ's
How do bearings increase efficiency?
Bearings reduce friction between moving parts in machinery, minimising energy loss. This reduction in friction enhances efficiency by allowing smooth movement and minimised heat generation.
How does a bearing affect performance?
Bearings significantly impact performance by providing stability and reducing resistance in moving parts. Properly functioning bearings ensure smoother operation, contributing to overall machinery performance.
What is the most efficient type of bearing?
The efficiency of a bearing depends on the application, but roller bearings, particularly tapered roller bearings, are known for their high load-carrying capacity and efficiency.
Can bearings contribute to energy savings in machines?
Yes, efficient bearings reduce friction, leading to energy savings in machines. The lower frictional resistance allows machinery to operate more smoothly, requiring less energy for movement and contributing to overall energy efficiency.