In the intricate machinery of modern industries, bearings play a pivotal role, serving as silent heroes that ensure smooth operations. Bearings have come a long way since their inception, evolving to meet the demands of advancing technologies. Initially, bearings were simple components designed to reduce friction between moving parts. The advent of ball bearings revolutionized the industry, providing enhanced efficiency and durability. This marked the beginning of a transformative era in the world of machinery.
Future of Bearing Technology
As we stand at the threshold of the future, the bearing industry is poised for remarkable transformations. The integration of advanced materials, precision engineering, and innovative designs is set to redefine the capabilities of bearings in various applications. The future promises not just incremental improvements but revolutionary changes that will shape the landscape of industries relying on these crucial components.
As we drive through the thrilling journey of bearings evolution, it’s only fair to pause and compare the stalwarts of the present with the game-changers of the future. Let’s dive into a side-by-side comparison of the existing bearings and the futuristic marvels waiting to reshape the landscape of machinery.
Benefits of Existing Technology Against Futuristic Technology?
Aspect |
Existing Bearings |
Futuristic Technology |
Friction Reduction |
Standard bearings excel at reducing friction but may require regular lubrication. |
Intelligent friction management in futuristic bearings minimizes wear and extends operational life without the need for constant maintenance. |
Materials |
Traditionally used metals and alloy components. |
Advanced materials like ceramics and composites enhance durability and performance. |
Design Complexity |
Limited customization, standard designs. |
3D-printed bearings offer unparalleled customization, allowing for intricate and optimized designs tailored to specific applications. |
Maintenance |
Requires regular lubrication making it maintenance intensive. |
Self-lubricating bearings eliminate the need for constant manual maintenance, reducing downtime and operational costs. |
Precision |
Focus on precision based output with industry standards. |
Unprecedented precision meets the demands of specialized applications, ensuring optimal performance. |
Sensors & Connectivity |
Limited to basic functionality without advanced sensing capabilities. |
Embedded sensors provide real-time data, enabling predictive maintenance and enhanced operational insights. |
Environmental Impact |
Varied, depending on lubrication and materials. |
Sustainable materials and reduced maintenance contribute to a more eco-friendly solution. |
Application Range |
Broad applications across industries. |
Bearings tailored for specific applications optimize performance and efficiency. |
Smart Bearing Technology
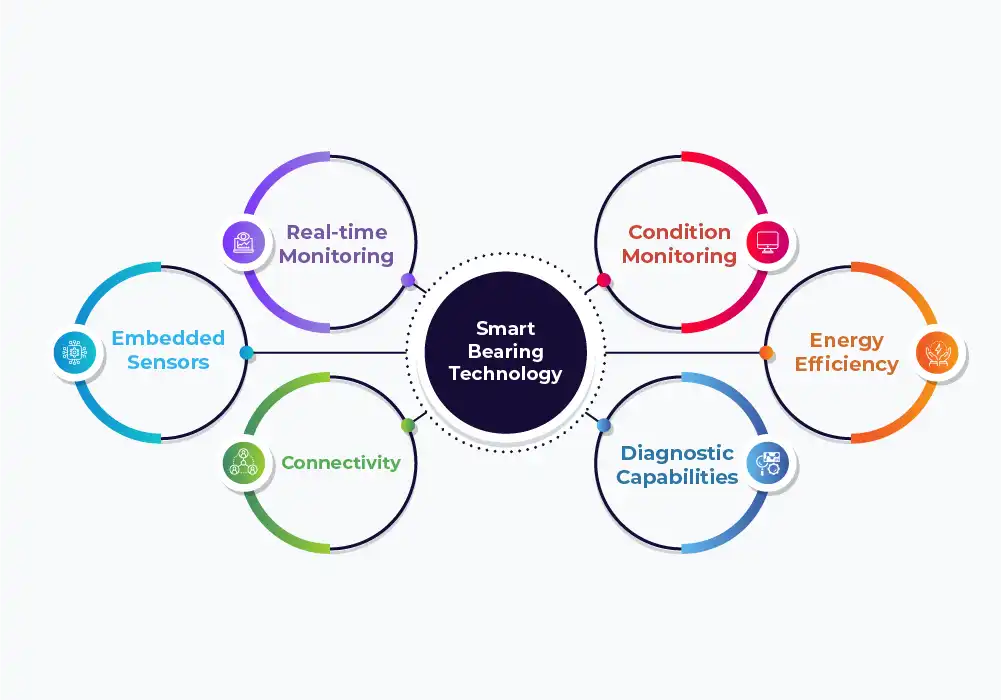
The era of intelligent machinery is dawning, and smart bearings are at its forefront. Equipped with sensors and connectivity features, smart bearings provide real-time data on their performance. This data can be leveraged for predictive maintenance, allowing businesses to preemptively address issues, minimize downtime, and optimize operational efficiency. Here are its significant features:
- Embedded Sensors: These monitor various parameters in real-time, collect data on temperature, vibration, load, and other critical factors directly affecting bearing performance.
- Real-time Monitoring: Continuous feedback on the bearing’s operational status, allows proactive monitoring. This in turn enables predictive analytics, to prepare for potential concerns and plan timely maintenance.
- Connectivity: Designed to integrate seamlessly with Internet of Things (IoT) platforms, it aims to empower operators to manage bearings from a central location remotely.
- Condition Monitoring: Smart bearings can assess their longevity, & create an early warning system to prevent unexpected failures.
- Energy Efficiency: The ability to adjust operational parameters based on real-time data contributes to energy efficiency. Proactive monitoring minimizes unexpected breakdowns, reducing the energy consumption associated with downtime.
- Diagnostic Capabilities: Smart bearings can diagnose faults and irregularities within the machinery, providing detailed insights into the root causes of issues. This is vital for the development of effective maintenance strategies.
3D Printed Bearings
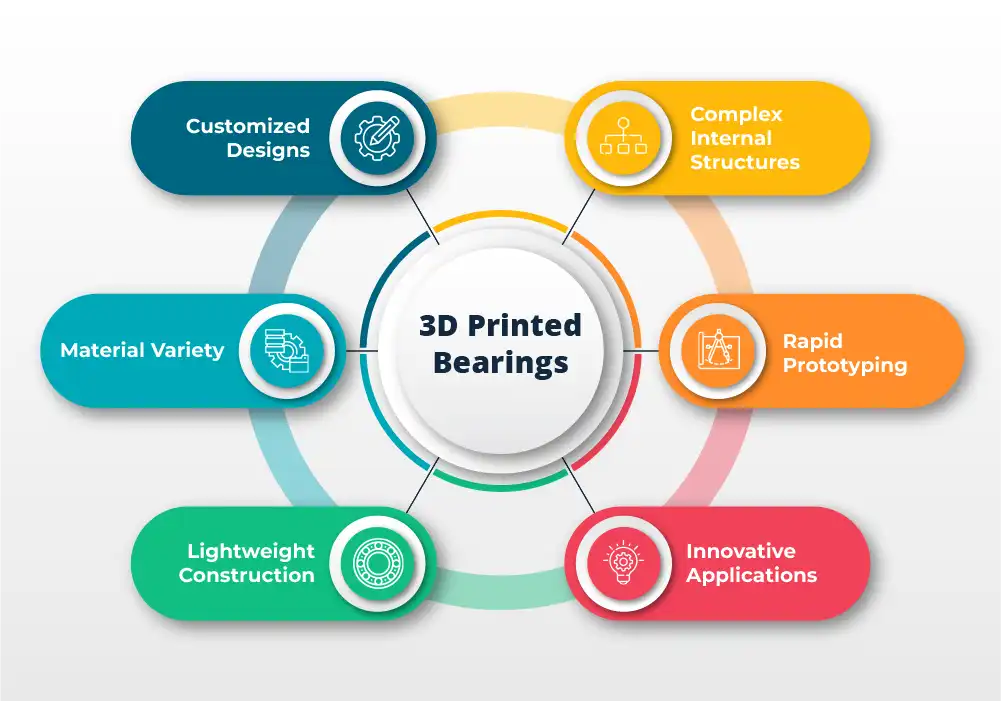
The advent of 3D printing has unleashed unprecedented possibilities in manufacturing, and bearings are no exception. 3D printed bearings offer customization like never before, allowing for intricate designs and geometries that were once thought impossible. This not only streamlines the production process but also opens doors to creating bearings tailored for specific applications, optimizing performance and longevity. Here are its significant features.
- Customized Designs: 3D printing allows for the creation of bearings with intricate and customized geometries, that precisely fit unique machinery requirements.
- Material Variety: 3D printing supports the use of various materials. Composite materials help create hybrid bearings for enhanced performance.
- Lightweight Construction: 3D printed bearings can be designed with lightweight structures without compromising strength. Ideal for applications where mobility and agility are critical.
- Complex Internal Structures: 3D printing allows for the creation of complex internal structures within bearings, optimizing load distribution and reducing stress points.
- Rapid Prototyping: This means quick iterations and modifications during the design phase, resulting in reduced development costs and better outcomes, especially for large bearings.
- Innovative Applications: Unconventional Shapes can be achieved with 3D printing. This opens up possibilities for innovative applications.
Self-Lubricating Bearings
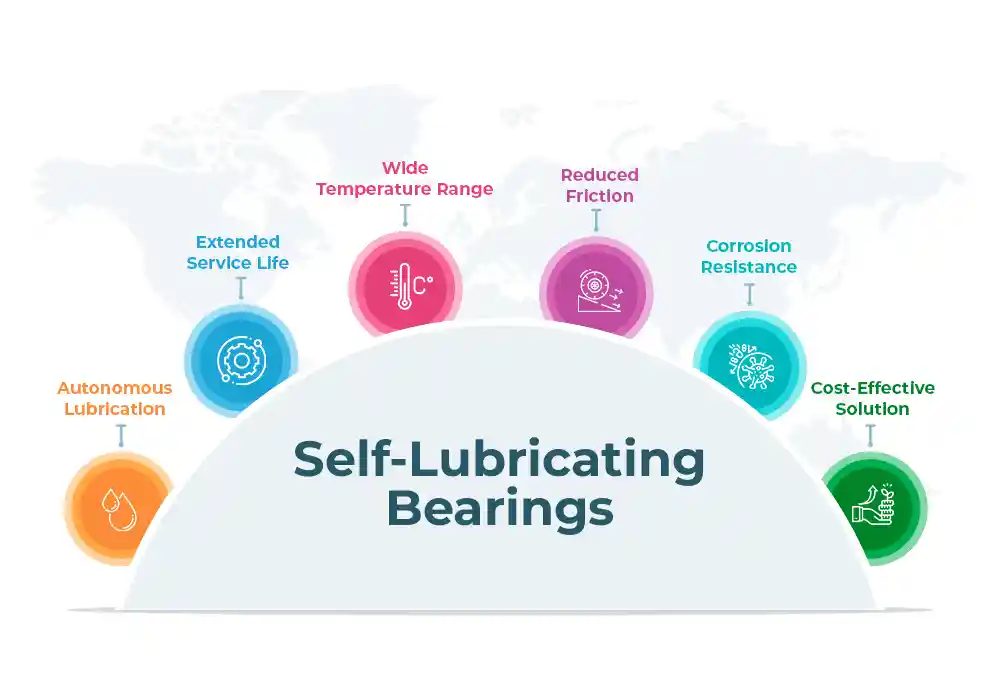
One of the most significant challenges in traditional bearings is the need for regular lubrication. Self-lubricating bearings is the solution that eliminates the hassle of manual lubrication. Equipped with embedded lubricants, it reduces friction and wear. This enhances efficiency while extending the lifespan of the bearing, making it a sustainable and cost-effective choice. Here are some of its marked features:
- Autonomous Lubrication: These come with built-in lubrication systems that ensure a continuous supply of lubricant to critical contact points. This means no external intervention is necessary for further lubrication.
- Extended Service Life: Clearly with a reduction in maintenance scheduling, lubrication is available right when the bearing needs it. This eliminates chances of friction completely, even in the hard to reach areas.
- Wide Temperature Range: With timely lubrication, bearings can sustain performance even in extreme temperature conditions.
- Reduced Friction: This directly translates to smooth and quiet operation, with no vibrations. This contributes to enhanced machinery performance.
- Corrosion Resistance: Self-lubricating provides a protective barrier against corrosion and harsh environmental conditions, i.e., exposure to moisture and chemicals.
- Cost-Effective Solution: Eliminates the need for frequent maintenance and manual lubrication, resulting in less frequent replacement, further reducing overall costs.
Precision Bearings
In the pursuit of optimal performance, precision bearings stand out as a beacon of excellence. These bearings are crafted with meticulous attention to detail, ensuring minimal tolerance and maximum accuracy. The demand for precision bearings is soaring across industries where even the slightest deviation can lead to significant consequences. From aerospace to medical devices, precision bearings are driving advancements in technology. Here are some of its distinct features:
- Minimal Deviation Tolerance: Consistent dimensional accuracy across multiple bearings ensures uniform and consistent bearings performance.
- High-Speed Capability: Reduced internal friction ensures efficiency at high rotational speeds, as in case of machine tools and aerospace components.
- Rigidity and Stiffness: Superior rigidity, minimized load deflection helps maintain operational accuracy and stability.
- Quiet Operation: These bearings operate with minimal noise and vibration, hence preferred for medical devices and laboratory equipment.
- Customizable Configurations: Configurations for precision bearings can be adapted as per the specialized needs in industries like aerospace, automotive, or medical devices.
- High-Quality Materials: Precision bearings use high-quality materials such as chrome steel, ceramic, or stainless steel.
- Corrosion Resistance: Due to their precision it eliminates unnecessary friction, ensures longevity and efficiency even in demanding environments.
- Quality Assurance: Rigorous testing is carried out to meet stringent quality standards to keep the bearing performance at optimum.
In conclusion, the future of bearing technology is an exciting landscape where innovation and functionality converge. The future promises not just incremental improvements but a complete reimagining of what bearings can achieve. As industries embrace these advancements, the future of bearings technology is set to redefine the very essence of industrial operations. As we compare the existing bearings with the futuristic marvels awaiting us, it’s clear that we’re on the brink of a technological revolution.