Introduction to Conveyor Rollers and Bearings
Conveyor systems are integral to modern industrial processes, ensuring the smooth and efficient transportation of materials. At the heart of these systems are conveyor rollers, which facilitate the movement of goods across various points in a facility. Bearings play a crucial role in the functioning of these rollers, enabling smooth operation and effective load handling. Without high-quality bearings, conveyor rollers would face increased friction and wear, leading to frequent maintenance and operational downtimes.
Types of Bearings Used in Conveyor Rollers
Different types of bearings are utilized in conveyor rollers to cater to various load and performance requirements. Understanding these types helps in selecting the right bearing for specific applications.
Bearing | Description | Advantages | Considerations |
Ball Bearings | Ball bearings use spherical balls to maintain the separation between the bearing races. | They offer low friction, high speed capabilities, and can handle both radial and axial loads. | They are suitable for applications where high speeds and low friction are critical. |
Roller Bearings | Roller bearings use cylindrical rollers instead of balls to maintain separation between bearing races. | They have a higher load-carrying capacity than ball bearings due to the larger contact area. | Ideal for applications involving heavy loads and moderate speeds. |
Sleeve Bearings | Sleeve bearings, also known as bushings, consist of a cylindrical sleeve that supports the rotating shaft. | They are simple in design, cost-effective, and suitable for low-speed applications. | Best for applications where cost and simplicity are prioritized over high-speed performance. |
Application of Conveyor Rollers across Industries
Conveyor rollers equipped with bearings are employed in a wide range of industries and applications due to their versatility and efficiency.
Manufacturing
- Application: In automotive assembly lines, conveyor rollers facilitate the movement of car parts from one workstation to another.
- Benefits: Ensure smooth and continuous operation, reducing manual handling and improving production efficiency.
Distribution Centers
- Application: Distribution centers use conveyor rollers to transport packages quickly and efficiently across different sorting and processing areas.
- Benefits: Enhance sorting speed and accuracy, ensuring timely delivery of goods. Airports.
Warehouses
- Application: Warehouses use conveyor rollers for moving inventory from storage areas to shipping docks.
- Benefits: Optimize space utilization and streamline the order fulfillment process.
Logistics and Aerospace
- Application: Baggage handling systems at airports rely on conveyor rollers to transport luggage from check-in counters to aircraft loading bays.
- Benefits: Improve passenger experience by ensuring quick and reliable baggage handling.
Maintenance and Lubrication Practices
Proper maintenance and lubrication of conveyor roller bearings are vital to ensure optimal performance and longevity. Here are some guidelines that can be followed and implemented overall to improve the effectiveness of the tasks and improve shelf life of the machinery. :
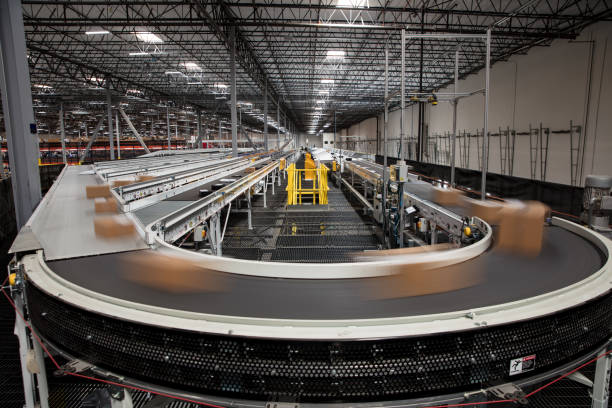
Impact of Bearing Performance on Conveyor Efficiency
The performance of bearings directly influences the efficiency, productivity, and operating costs of conveyor systems.
Enhanced Efficiency
- Impact: High-quality bearings reduce friction, allowing conveyor rollers to operate smoothly and efficiently.
- Example: In a distribution center, smooth-operating bearings enable faster sorting and handling of packages.
Increased Productivity
- Impact: Reliable bearings minimize downtime caused by maintenance and repairs.
- Example: In a manufacturing plant, reduced downtime leads to continuous production cycles and higher output.
Reduced Operating Costs
- Impact: Efficient bearings decrease energy consumption and reduce wear on other conveyor components.
- Example: In a warehouse, lower energy consumption translates to cost savings in utility bills.
Selecting High-Quality Bearings and Implementing Effective Maintenance Practices
To maximize conveyor uptime, selecting high-quality bearings and implementing effective maintenance practices are essential.
- Quality Selection: Choose bearings from reputable manufacturers known for their quality and reliability.
- Custom Solutions: Consider custom bearings designed for specific applications to ensure optimal performance.
- Training: Provide proper training for maintenance personnel on bearing inspection, lubrication, and replacement techniques.
Conclusion
Bearings are integral to the efficient and smooth operation of conveyor rollers, impacting everything from load handling to overall system productivity. Understanding the different types of bearings used in conveyor rollers, their applications, and maintenance practices can significantly enhance conveyor performance and reliability. By selecting high-quality bearings and implementing effective maintenance routines, industries can maximize uptime, reduce operating costs, and ensure the longevity of their conveyor systems.
FAQ's
What are the bearings used in rollers?
Bearings used in rollers include ball bearings, roller bearings, and sleeve bearings. Each type serves different load and speed requirements, ensuring smooth operation and longevity of conveyor systems.
What is the most common roller bearing?
The most common roller bearing used in conveyor rollers is the ball bearing. It offers low friction, high-speed capabilities, and can handle both radial and axial loads, making it versatile for various applications.
What are bearing rollers made of?
Bearing rollers are typically made of materials such as steel, stainless steel, or ceramic. The choice of material depends on the application, load requirements, and operating environment.
Which bearing is used in screw conveyor?
In screw conveyors, roller bearings or spherical roller bearings are commonly used due to their ability to handle heavy radial and axial loads, ensuring reliable operation in demanding conditions.
Which rollers are used in conveyors?
Conveyors use various types of rollers, including gravity rollers, driven rollers, and idler rollers. Each type is designed to meet specific handling and operational requirements in different conveyor systems.
What is the standard size of a roller conveyor?
The standard size of a roller conveyor varies based on the application. Common diameters range from 1.5 inches to 3.5 inches, with lengths and widths customized to fit specific operational needs.
How do conveyor rollers work?
Conveyor rollers work by rotating around a central shaft, allowing materials to move along the conveyor belt or frame. Bearings within the rollers reduce friction, enabling smooth and efficient transportation of goods.
What is the formula for a conveyor roller?
The formula for calculating the length of a conveyor roller is: Roller Length = Frame Width – (2 x Bearing Width). This ensures the roller fits correctly within the conveyor frame, allowing for optimal operation.