In the realm of precision engineering, the choice of bearing steels holds paramount importance in determining the performance, durability, and reliability of bearings. Bearing steels are specially engineered alloys designed to withstand the rigorous demands of rotating machinery, providing essential properties such as wear resistance, corrosion resistance, and superior fatigue strength.
Understanding Bearing Steels
Bearing steels are meticulously formulated alloys known for their exceptional mechanical properties, tailored to meet the rigorous demands of bearing applications. These steels exhibit superior wear resistance, enabling bearings to withstand the abrasive forces encountered during operation.
Additionally, they offer excellent corrosion resistance, safeguarding bearings against degradation in harsh operating environments. Furthermore, bearing steels boast superior fatigue strength, ensuring prolonged service life and reliable performance under cyclic loading conditions.
Types of Bearing Steels:
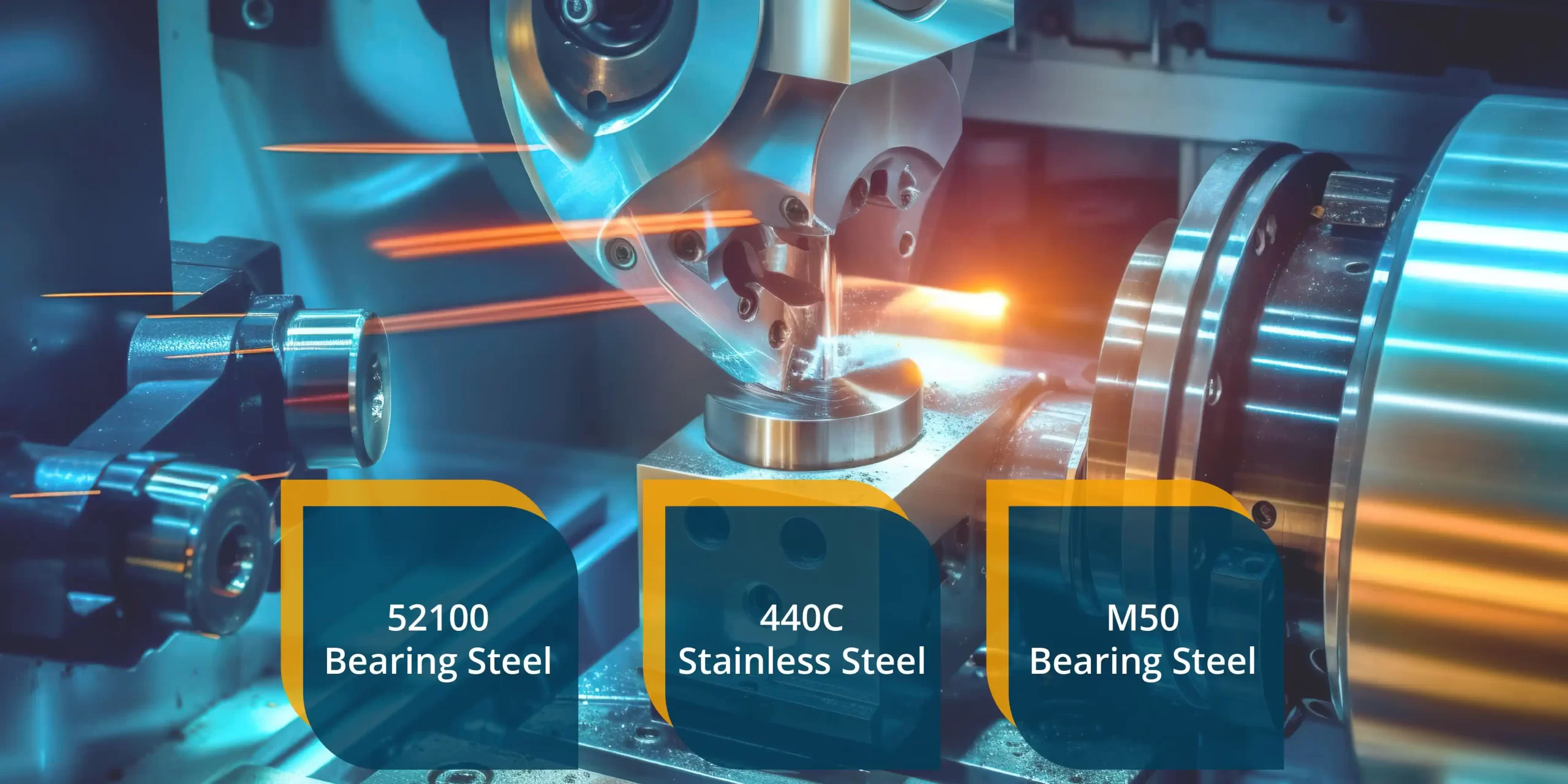
Several types of bearing steels are commonly employed in manufacturing, each offering distinct properties and advantages. Among the most widely used bearing steels are:
- 52100 Bearing Steel: Renowned for its high carbon content and exceptional hardness, 52100 bearing steel is a popular choice for various bearing applications. It offers excellent wear resistance and fatigue strength, making it suitable for demanding operating conditions.
- 440C Stainless Steel: Known for its corrosion resistance and high hardness, 440C stainless steel is often utilised in applications where resistance to rust and corrosion is paramount. It offers superior durability and reliability in corrosive environments.
- M50 Bearing Steel: Recognized for its high temperature resistance and superior wear properties, M50 bearing steel is commonly used in aerospace and high-speed bearing applications. It provides exceptional performance under extreme operating conditions.
Manufacturing Processes for Bearing Steels:
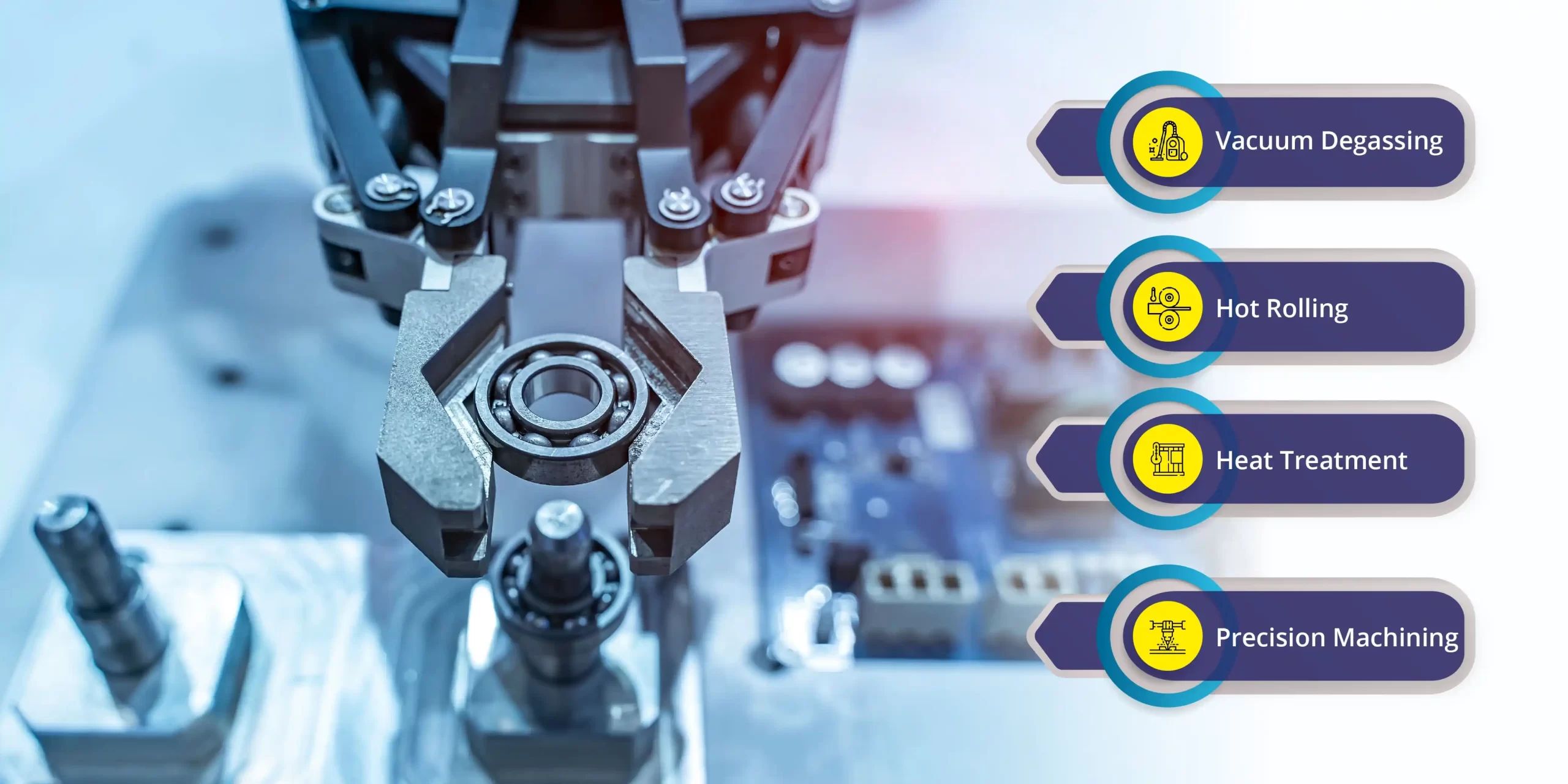
Bearing steels undergo specialised manufacturing processes to achieve the desired properties and characteristics. These processes may include:
- Vacuum Degassing: Removes impurities and gases from the steel, ensuring high purity and uniformity.
- Hot Rolling: Shapes the steel into desired forms and sizes, enhancing its mechanical properties.
- Heat Treatment: Utilises precise heating and cooling cycles to optimise the steel’s microstructure and properties.
- Precision Machining: Achieves tight tolerances and surface finish requirements for bearing components.
Role of Bearing Steels in Quality Bearing Manufacturing
Bearing steels play a pivotal role in quality bearing manufacturing by providing the essential mechanical properties required for reliable performance and longevity. From the inner and outer rings to the rolling elements and cages, every component of a bearing relies on the inherent properties of bearing steels to withstand the demands of rotating machinery. The selection of the appropriate bearing steel grade and manufacturing processes is crucial in ensuring the highest standards of precision, durability, and reliability in bearings.
FAQ's
What steel is used for bearings?
Bearing steels such as 52100, 440C stainless steel, and M50 bearing steel are commonly used for bearings due to their superior mechanical properties and performance characteristics
What is the best bearing steel?
The best bearing steel depends on the specific requirements of the application. However, 52100 bearing steel is widely regarded as one of the most versatile and reliable choices for general-purpose bearings.
What is 52100 bearing steel?
52100 bearing steel is a high carbon alloy steel renowned for
- its exceptional hardness,
- its wear resistance, and
- fatigue strength
Therefore the 52100 steel has all the properties that makes it ideal for various bearing applications.
What is bearing material?
Bearing material refers to the type of steel or alloy used to manufacture bearings. It is chosen based on the specific requirements of the application, such as load capacity, operating conditions, and environmental factors.
Why is steel used for bearings?
Steel is commonly used for bearings due to its excellent mechanical properties, including high hardness, strength, and wear resistance. These properties enable bearings to withstand the rigorous demands of rotating machinery and provide reliable performance over extended periods.
How strong is bearing steel?
Bearing steel is known for its exceptional strength and durability, capable of withstanding high loads and operating conditions without deformation or failure. The strength of bearing steel depends on factors such as alloy composition, heat treatment, and manufacturing processes.