Whether you’re cruising down the highway or navigating rough terrain, your vehicle’s wheel bearings play a crucial role in ensuring smooth and efficient rotation. Understanding how to maximize their lifespan and enhance performance is essential for a safe and enjoyable driving experience. Here are five essential steps to help you achieve just that:
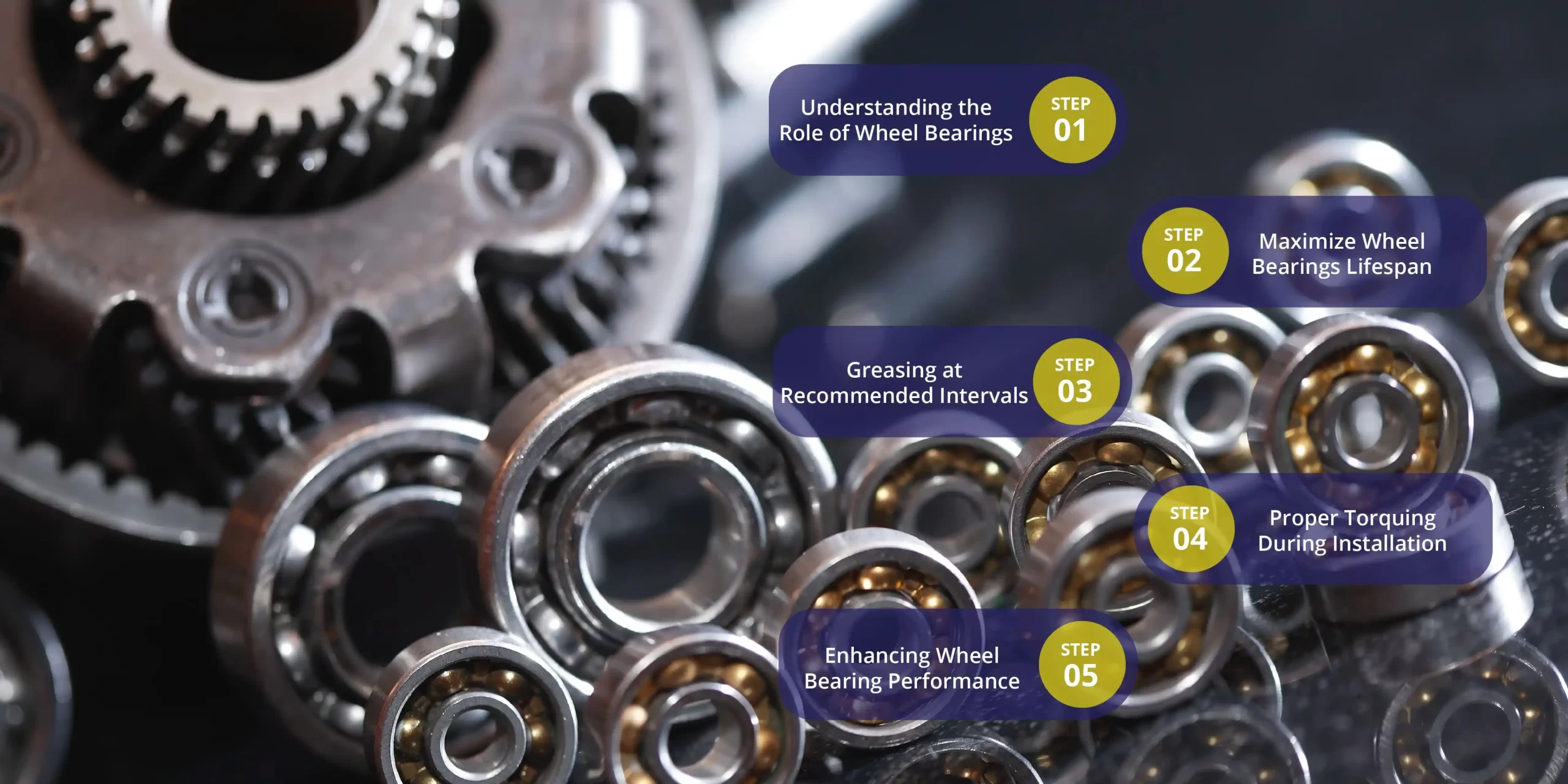
Step 1: Understanding the Role of Wheel Bearings
Wheel bearings are critical components located within the wheel hub assembly of your vehicle.
- They enable the wheels to rotate smoothly,
- Support the vehicle’s weight, and
- Absorbs various shocks and impacts encountered during driving.
Without properly functioning wheel bearings, your vehicle’s handling, stability, and safety could be compromised.
Step 2: Maximize Wheel Bearings Lifespan
Now that we understand the importance of wheel bearings the next step is to help ensure it lasts long. Here are some things that can ensure this:
- Proper Torquing During Installation: Ensure that wheel bearings are installed with the correct torque specifications to prevent overloading or underloading, which can lead to premature failure.
- Regular Inspection: Periodically inspect your wheel bearings for signs of wear, such as excessive noise, vibration, or play in the wheel.
- Periodical Greasing: At recommended Intervals, proper lubrication is vital for reducing friction and preventing premature wear. Follow the manufacturer’s recommendations for greasing intervals, especially after driving through water or off-road conditions.
- Avoid Overloading: This will not help in the proper usage of the bearings as there will be too much pressure.
- Maintain Wheel Alignment: This will also help immensely, as the wheel will stay balanced and not affect the performance of the bearings.
Step 3: Greasing at Recommended Intervals
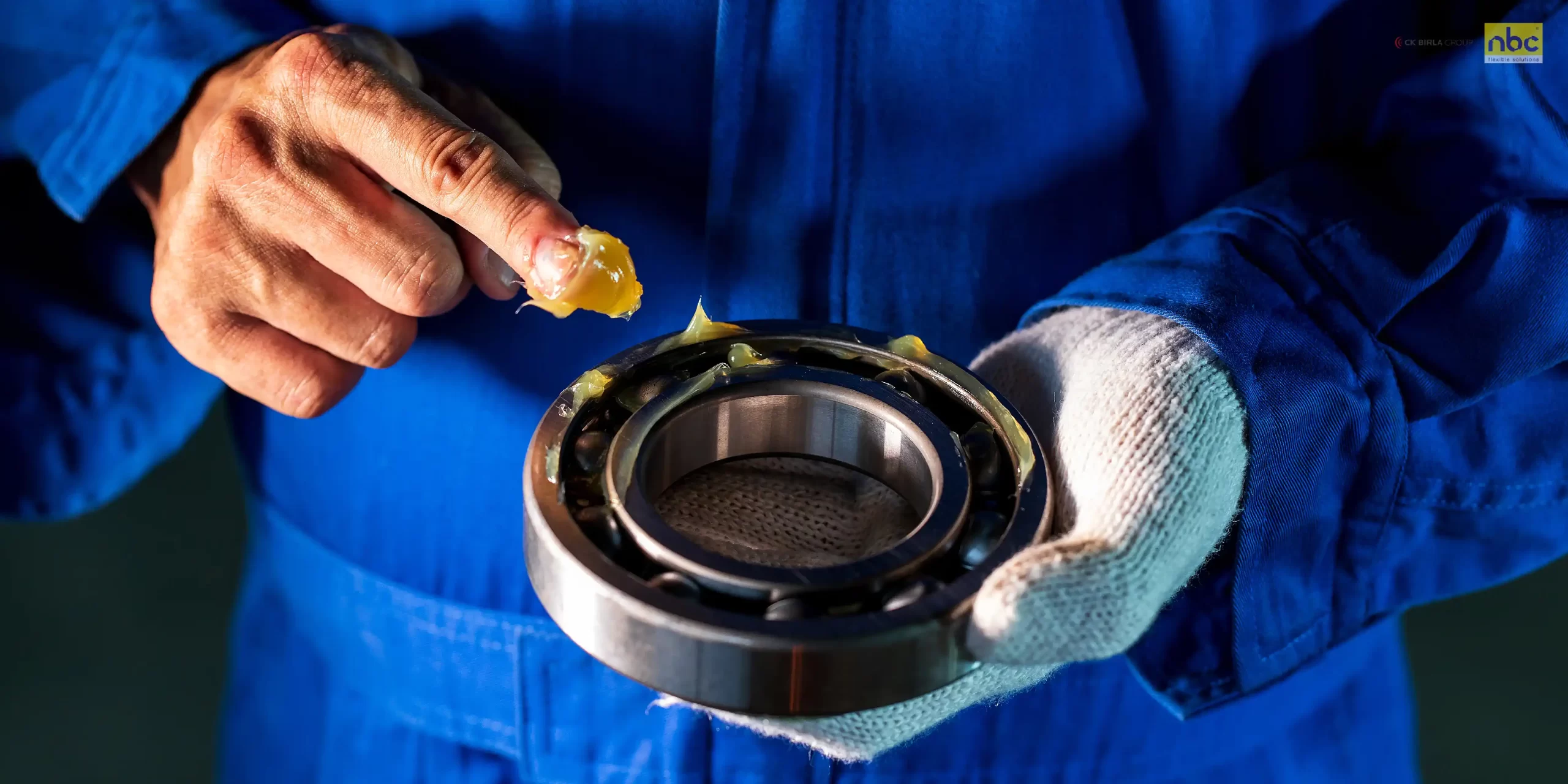
- Regular greasing is essential for maintaining optimal performance and extending the lifespan of your wheel bearings.
- Use a high-quality, lithium-based grease recommended by the manufacturer and apply it according to the specified intervals.
- Pay special attention to greasing after exposure to water, mud, or harsh environmental conditions, as these can accelerate wear and corrosion.
Step 4: Proper Torquing During Installation
Wheel bearings are installed as per the manufacturer’s specifications using a calibrated torque wrench. This needs proper care.
- Over-tightening can increase friction and stress on the bearings, leading to premature wear.
- Under-tightening can cause excessive play and instability in the wheel assembly.
Follow the recommended torque values and sequence provided in the vehicle’s service manual to ensure proper installation.
Step 5: Enhancing Wheel Bearing Performance
Apart from the basic essentials like lubrication and installation, over time the performance of the bearings are dependent upon how they are used.
- Overloading can lead to premature failure: Avoid overloading your vehicle beyond its recommended capacity, as this can put excessive strain on the wheel bearings and lead to premature failure.
- Wheel misalignment will also lead to wear: Improper wheel alignment can cause uneven wear and loading on the wheel bearings, affecting their performance and lifespan. Regularly check and adjust wheel alignment as needed to ensure even tire wear and optimal bearing operation.
By following these five essential steps, you can maximize the lifespan of your wheel bearings and enhance their performance for a smoother and safer driving experience. Regular maintenance, proper greasing, correct torquing during installation, and avoiding overloading are key factors in ensuring the longevity and reliability of your vehicle’s wheel bearings. Stay vigilant for signs of wear and address any issues promptly to keep your vehicle running smoothly on the road ahead.
FAQ's
How often should wheel bearings be replaced?
Wheel bearings typically last around 100,000 to 150,000 miles under normal driving conditions. However, factors such as driving habits, road conditions, and vehicle maintenance can affect their lifespan. It’s essential to monitor for signs of wear and replace wheel bearings as needed to ensure safe operation.
How long will a worn wheel bearing last?
A worn wheel bearing can last anywhere from a few hundred miles to several thousand miles, depending on the extent of the wear and driving conditions. However, driving with a worn wheel bearing can be dangerous and may lead to further damage to the vehicle’s suspension and steering components.
How do I know when my wheel bearings need replacing?
Signs of a bad wheel bearing include unusual noises such as grinding, humming, or growling coming from the wheels, excessive play or looseness in the wheel assembly, and uneven tire wear. If you notice any of these symptoms, it’s essential to have your wheel bearings inspected and replaced by a qualified mechanic.
What are the signs of a bad wheel bearing?
- Uncommon wheel noises like grinding, humming, or growling.
- Excessive play or looseness in the wheel assembly
- Vibration or shimmying in the steering wheel
- Uneven tire wear
If you experience any of these symptoms, it’s crucial to have your wheel bearings inspected and replaced if necessary to ensure safe driving.