A factory that works on a fixed set of machinery, comes with its unique musical chimes and beats. Some of it is attributed to the noise of the mechanical components that are moving one part to another, while others are not so welcome noises that tend to indicate some sort of an unresolved problem that needs to be addressed. In most cases, these distressing or disturbing noises are attributed to noisy bearings.
Understanding the causes, effects, and solutions to bearing noise is crucial for maintaining optimal performance and prolonging the lifespan of equipment.
What Leads to Noisy Bearings?
Bearing noise can be a persistent nuisance, signaling potential issues that demand attention. Some of the main causes of noisy bearings are:
- Lack of lubrication: Insufficient or improper lubrication paves way for increased friction and wear within the bearing, resulting in bearing noise.
- Contamination: Foreign particles such as dirt, dust, or debris that might have infiltrated into the bearing, causing friction and noise during operation.
- Misalignment: This is a major problem that might lead to significant downtime. Misalignment of bearing components causes uneven loading and excessive wear, impacting the lifespan of bearings.
- Overloading: Excessive loads that are beyond the bearing’s load bearing capacity can accelerate wear and noise.
- Defective components: Faulty or worn-out bearing components, such as balls, rollers, or raceways, can lead to noise during rotation. This signifies poor maintenance and inadequate lubrication.
What Should You Do if Your Bearing Starts Making Noise?
Noisy bearings are a common phenomenon in factories and places which operate heavy machinery and equipment. But the key lies in identifying it and rectifying the problem ahead. Here’s what you should ideally do to check your bearings for noises:
- Diagnose the source: Identify the root cause of the noise by inspecting the bearing and surrounding components.
- Address lubrication issues: Ensure proper lubrication levels by using high-quality reliable lubricants that are suitable for the application.
- Clean and inspect: Remove any contamination or debris from the bearing. Sometimes the housing tends to store the debris leading to unnecessary stress on the bearing. Additionally, inspect for signs of wear or damage caused by the stored debris.
- Check for misalignment: Verify that the bearing components are properly aligned. Sometimes an initial unnoticed misalignment can snowball into a bigger and noisier bottleneck in the process.
- Monitor performance: Regularly monitoring overall performance and addressing any abnormal noise can prevent further damage.
What is the Impact of Bearing Noise?
Bearings usually tend to outlive their machines when used and maintained properly. But there is always a 10% margin of defect where the bearings can start showing problems by turning noisy.
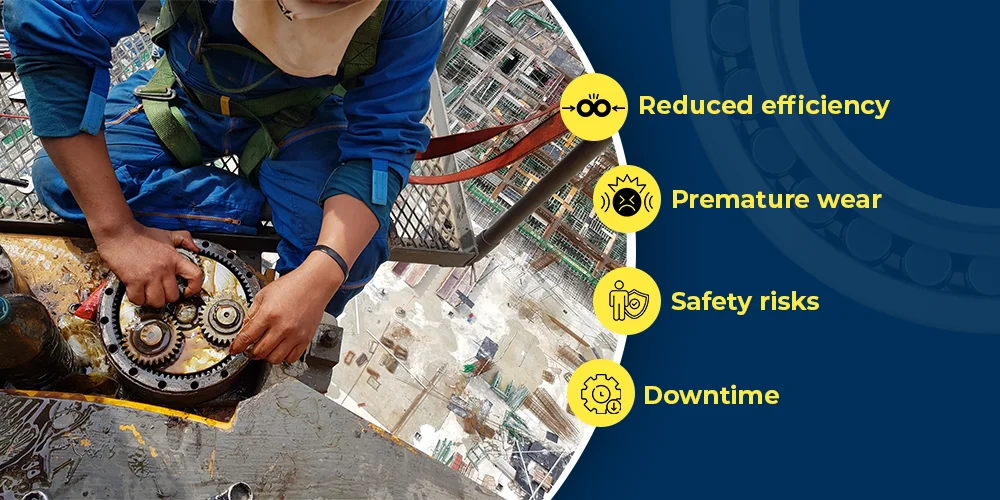
Though a very small component in the machinery, noisy bearings can lead to:
- Reduced efficiency: Increased friction and energy loss due to noise ends in decreased efficiency and higher operating costs.
- Premature wear: Noise is a precursor to mechanical wear and component failure.
- Safety risks: Unaddressed bearing noise can escalate into more severe issues, posing safety hazards to operators and workers.
- Downtime: Equipment downtime can disrupt operations, causing production delays and financial losses.
Can Bearing Noise Issues Be Prevented?
Yes, proactive maintenance practices and proper installation techniques can help prevent bearing noise issues.
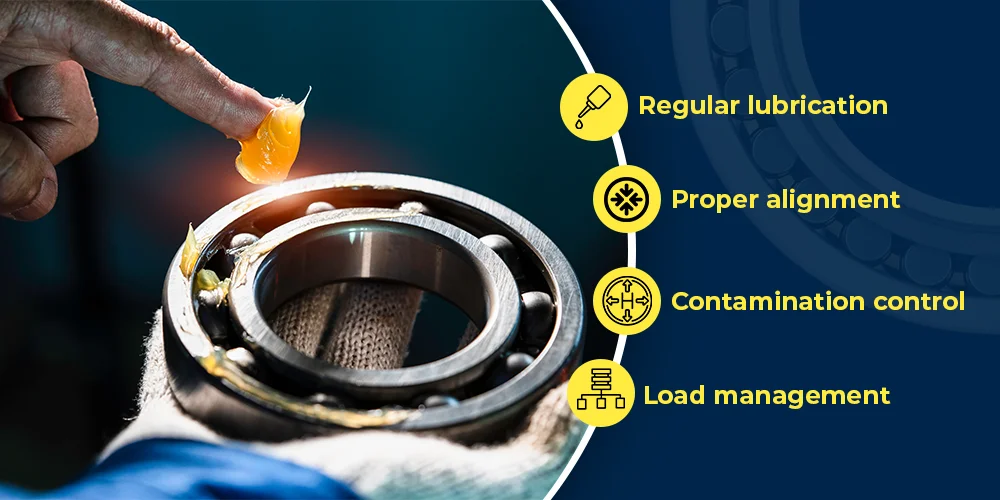
- Regular lubrication: Implementing a lubrication schedule with quality lubricants can minimize friction and reduce noise levels.
- Proper alignment: Accurate alignment can prevent excessive wear and noise generation substantially.
- Contamination control: Use proper sealing arrangements and housing design to prevent ingress of debris and other contaminants.
- Load management: Overloading always leads to premature wear and noise, hence avoid going beyond capacity.
What Are the Other Factors That Prevent Bearing Noise?
- Ensure routine inspections to detect early signs of wear or damage.
- Provide training to personnel on proper bearing installation, maintenance, and troubleshooting techniques.
- Invest in high-quality bearings from reputable manufacturers to ensure reliability and performance.
- Adopt predictive maintenance techniques, like vibration analysis and thermal monitoring, to detect bearing issues before they escalate.
Conclusion
In conclusion, understanding the causes, effects, and solutions to bearing noise is essential for optimizing equipment performance and ensuring reliable operation. By implementing proactive maintenance practices and addressing noise issues promptly, businesses can minimize downtime, reduce repair costs, and extend the lifespan of their machinery.
FAQ's
Can misalignment affect bearing noise?
Yes, misalignment can lead to uneven loading and increased friction, resulting in abnormal noise levels in bearings.
How important is monitoring for addressing bearing noise?
Monitoring is crucial as it allows for early detection of bearing issues, enabling timely intervention to prevent further damage and downtime.
Can noise issues in bearings be resolved without replacing the entire bearing?
In some cases, noise issues can be addressed through corrective measures such as lubrication, cleaning, and realignment, without requiring bearing replacement.
How critical is addressing bearing noise for overall machinery performance?
Addressing bearing noise is essential for maintaining overall machinery performance, as it can impact efficiency, safety, and reliability.